Nippon Paint Automotive Coatings Co., Ltd. (NPAC) and Uchihamakasei Corp. are at the forefront of innovation in automotive manufacturing, having jointly developed Japan’s first in-mould coating (IMC) technology for large automotive exterior parts. This breakthrough promises a more sustainable, efficient, and aesthetically versatile future for vehicle production.
How In-Mould Coating Works
This new process represents a significant leap forward by seamlessly integrating resin moulding and surface coating. Instead of using separate spraying and drying steps, manufacturers inject paint directly into the mould after forming the resin component. This approach results in a flawless, high-quality coating that becomes an essential part of the moulding process.
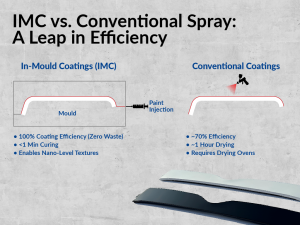
Environmental Benefits: A Greener Approach
Uchihamakasei estimates that this ingenious method slashes CO₂ emissions by an impressive 60% and dramatically reduces Volatile Organic Compound (VOC) emissions. NPAC’s contribution is key: they’ve developed an advanced, solvent-free paint that makes this possible. This paint alone achieves a 99% or more significant reduction in VOC emissions, significantly contributing to cleaner manufacturing.
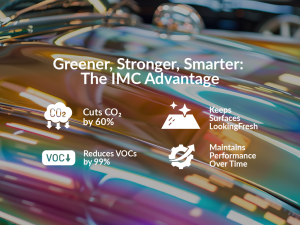
Quality and Design Enhancements: Beyond Sustainability
The in-mould coating process isn’t just about being green; it also significantly enhances automotive exteriors’ quality and design capabilities.
- Superior Finish: It creates a smoother surface finish than traditional spray coating.
- Design Precision: The process ensures greater accuracy in reproducing designs.
- Unlocking New Aesthetics: Crucially, it unlocks the potential for complex and visually striking designs. Intricate geometric patterns, embossed finishes, and even iridescent colours – previously challenging or impossible with spray coating – are now achievable.
The Collaborative Process This groundbreaking technology is the result of a close partnership. The companies have also optimised the resin and catalyst properties and refined the coatings to work seamlessly within the in-mould process.
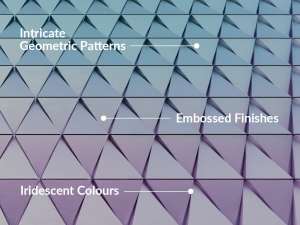
Key Advantages
To recap, here’s a breakdown of the core benefits:
- Sustainability Boost: Significantly lowers CO₂ and VOC emissions.
- Efficiency Gains: Combines moulding and coating into a single step, eliminating separate spray booths and drying ovens.
- Enhanced Quality: Delivers superior surface smoothness, improves design accuracy, and reduces defects.
- Design Revolution: Enables complex, high-value designs, expanding the possibilities for car aesthetics.
Future Outlook
NPAC and Uchihamakasei are committed to making this technology available to car manufacturers, paving the way for its adoption in mass-produced vehicles. Companies will continue to refine their technology, striving for the least environmental impact from automobile manufacturing. This collaboration represents a significant step towards a more sustainable and visually exciting future for the automotive industry.